Mastering Industrial Hygiene: A How-To Guide for Cleaning Your Facility in Orange County
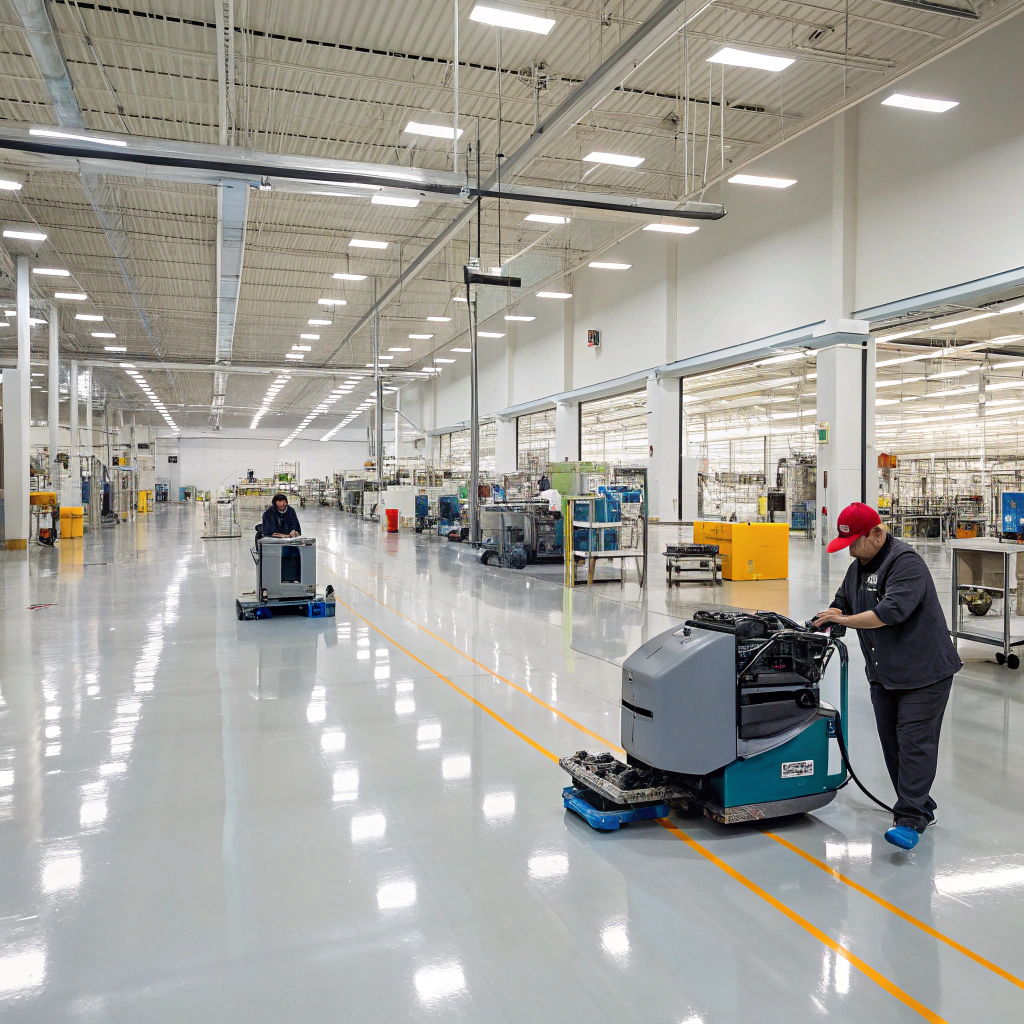
You’ll quickly uncover that maintaining a clean industrial facility in Orange County isn’t just about appearances—it’s about operational efficiency, safety compliance, and protecting your investment. Whether you’re dealing with stubborn oil stains on warehouse floors or managing hazardous material cleanup protocols, the unique challenges of industrial cleaning require specialized solutions and expertise. As regulations tighten and operational demands increase, you’ll need to understand how modern cleaning technologies and eco-friendly practices can transform your facility maintenance strategy. Let’s investigate how professional industrial cleaning services can help you overcome these complex challenges while staying within budget.
Common Industrial Cleaning Challenges
Industrial facilities face multiple cleaning obstacles that can impact operational efficiency and workplace safety.
You’ll routinely encounter heavy grease accumulation, oil spills, and chemical residues that require specialized cleaning protocols.
Equipment accessibility presents another significant challenge, as you must navigate around complex machinery while maintaining thorough cleaning standards.
The proper handling of hazardous waste demands strict compliance with local and federal regulations, requiring you to implement specific disposal procedures and documentation.
Machinery maintenance cleaning needs careful attention to prevent damage to sensitive components while ensuring thorough decontamination.
You’ll also need to manage high-traffic areas where dirt and debris accumulate rapidly, often requiring more frequent cleaning interventions.
Time constraints pose supplementary pressure, as cleaning must occur without disrupting production schedules or compromising operational workflows.
Professional Equipment and Technologies
Professional cleaning within industrial environments relies on specialized equipment engineered for heavy-duty applications.
You’ll need industrial-grade floor scrubbers, pressure washers rated at 3000+ PSI, and automated sweepers designed for continuous operation. These machines incorporate cleaning innovations like HEPA filtration systems and eco-friendly chemical dispensing units.
To maintain peak performance, you’ll want to implement regular equipment maintenance schedules. This includes daily inspection of mechanical components, cleaning of filters, and calibration of chemical dispensing systems.
Modern industrial cleaning technologies also feature IoT sensors that monitor machine performance and alert you to potential issues before they become critical failures.
Your investment in professional-grade equipment will require proper training for operators and adherence to manufacturer specifications for operation and servicing.
Safety Protocols and Compliance
Maintaining a safe cleaning operation in warehouses and industrial facilities requires strict adherence to OSHA guidelines and industry-specific safety protocols.
You’ll need to implement extensive employee training programs that cover proper handling of cleaning chemicals, equipment operation, and emergency response procedures.
Before beginning any cleaning task, you must conduct thorough hazard identification assessments to evaluate potential risks and establish appropriate control measures.
You’ll need to guarantee your staff regularly updates Safety Data Sheets (SDS), wears required Personal Protective Equipment (PPE), and follows proper chemical dilution ratios.
Create clear documentation of all safety procedures and maintain detailed incident reports to track and prevent future accidents.
Remember to post safety signage in visible locations and regularly inspect emergency eyewash stations and medical supplies to maintain compliance with current regulations.
Specialized Floor Care Services
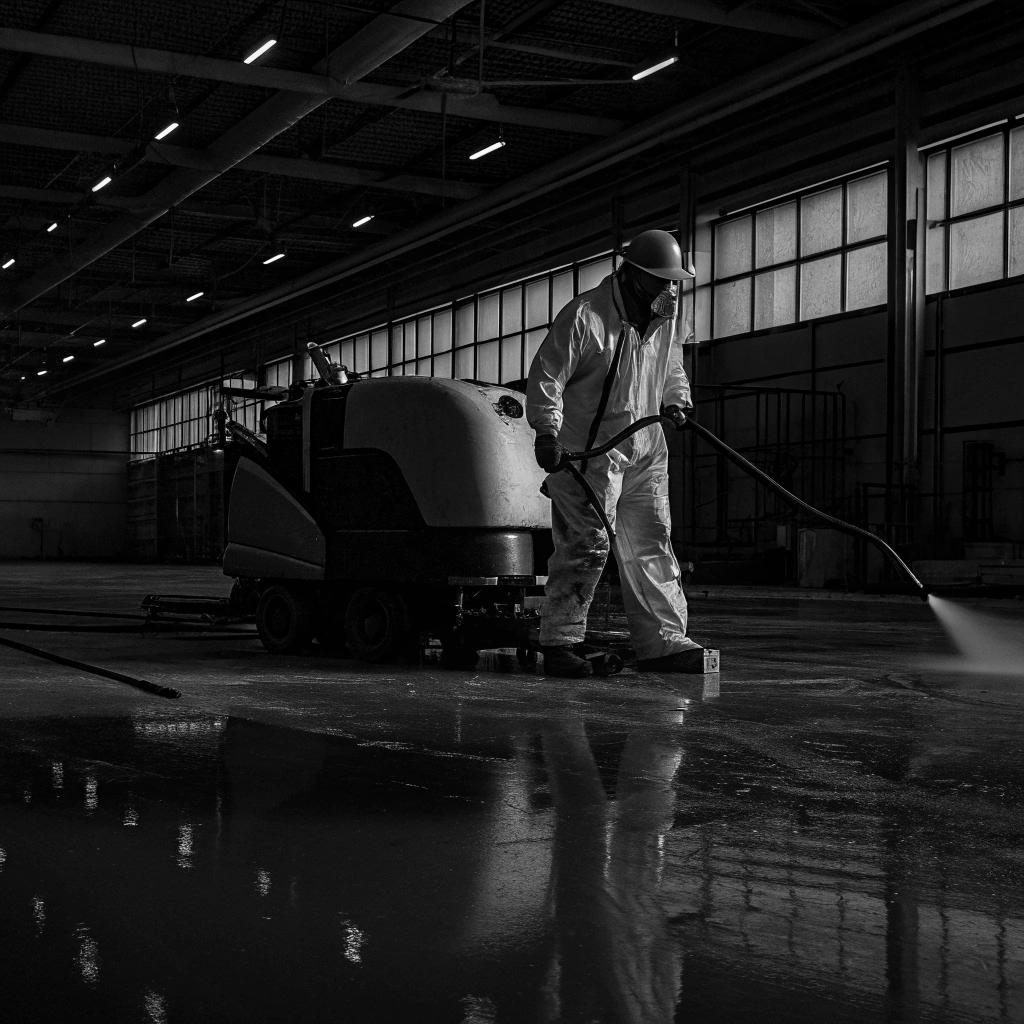
Diverse floor types in warehouse and industrial settings require specialized cleaning approaches tailored to their unique composition and usage patterns.
You’ll need to implement specific floor maintenance strategies based on whether you’re dealing with concrete, epoxy, vinyl, or other industrial surfaces.
For concrete floors, you’ll want to contemplate mechanical cleaning methods like scrubbing, stripping, and burnishing, combined with appropriate surface treatment options such as sealants or coatings.
When working with epoxy floors, you’ll need to use pH-neutral cleaners and avoid harsh chemicals that could compromise the coating’s integrity.
Vinyl composite tile (VCT) requires regular stripping and waxing to maintain its protective layer.
Your maintenance program should also account for high-traffic areas, chemical exposure zones, and loading docks where specialized treatments may be necessary.
High-Bay and Ceiling Cleaning
Upgraded industrial spaces present unique cleaning challenges that require specialized equipment and safety protocols for accessing high-bay ceilings, exposed ductwork, and overhead lighting fixtures.
You’ll need professional high bay maintenance services equipped with aerial lifts and specialized cleaning tools to effectively remove dust, cobwebs, and industrial residue from raised surfaces.
Certified technicians utilize telescoping poles and advanced vacuum systems to clean areas up to 40 feet high while maintaining ceiling accessibility.
Safety-rated lift equipment provides secure platforms for cleaning hard-to-reach lighting fixtures and HVAC components.
Industrial-grade cleaning solutions break down stubborn grease and grime without damaging structural materials.
Regular cleaning of high-bay areas improves air quality, reduces fire hazards, and maintains proper illumination levels.
You’ll benefit from scheduled maintenance programs that address both ground-level and raised cleaning needs systematically.
Green Cleaning for Industrial Spaces
While high-bay cleaning focuses on vertical reach and accessibility, modern industrial cleaning must also prioritize environmental responsibility.
You’ll need to implement sustainable practices that minimize environmental impact while maintaining rigorous cleaning standards. This includes using eco-friendly products that are biodegradable and phosphate-free, yet effective against industrial grime and contamination.
Consider integrating microfiber technology for improved dirt capture with reduced chemical usage, and implement water-efficient cleaning methods that decrease waste runoff.
You can optimize your cleaning schedule by using automated dosing systems to prevent chemical overuse. Select cleaning agents certified by recognized environmental standards, and train your staff in proper dilution ratios to maximize efficiency while reducing environmental impact.
These practices won’t just protect the environment—they’ll also improve workplace safety and reduce your operation’s carbon footprint.
Emergency Response Cleaning Services
Responding swiftly to industrial accidents and hazardous spills requires an extensive emergency cleaning protocol that you’ll need to establish before incidents occur.
When you’re faced with unexpected contamination events, proper spill containment becomes your top priority to prevent environmental damage and workplace hazards.
You’ll need a dedicated emergency response team trained in hazardous material handling, equipped with appropriate PPE and containment supplies.
Your facility must maintain an updated chemical inventory and corresponding safety data sheets (SDS) for quick identification and proper cleanup procedures.
You should establish clear evacuation routes and containment zones while implementing a communication system that alerts all necessary personnel.
Contact your certified emergency cleaning service immediately when an incident exceeds your team’s capabilities.
They’ll arrive with specialized equipment and expertise to manage complex contamination scenarios efficiently.
Cost Management and Scheduling
Beyond emergency response protocols, effective cost management and scheduling form the backbone of any industrial cleaning operation.
You’ll need to implement systematic budget optimization strategies while maintaining service quality. Start by analyzing your facility’s specific cleaning requirements and establishing clear maintenance intervals.
Your resource allocation should prioritize high-traffic areas and critical operational zones.
You’ll want to create detailed cleaning schedules that align with your production downtime to minimize disruptions. Consider implementing a digital tracking system to monitor labor hours, supply usage, and equipment maintenance costs.
Track your cleaning expenses against predetermined benchmarks, and adjust your protocols as needed.
To enhance efficiency, you should develop contingency plans for unexpected cleaning needs while maintaining your regular maintenance schedule. This approach guarantees both cost control and operational continuity.
Conclusion
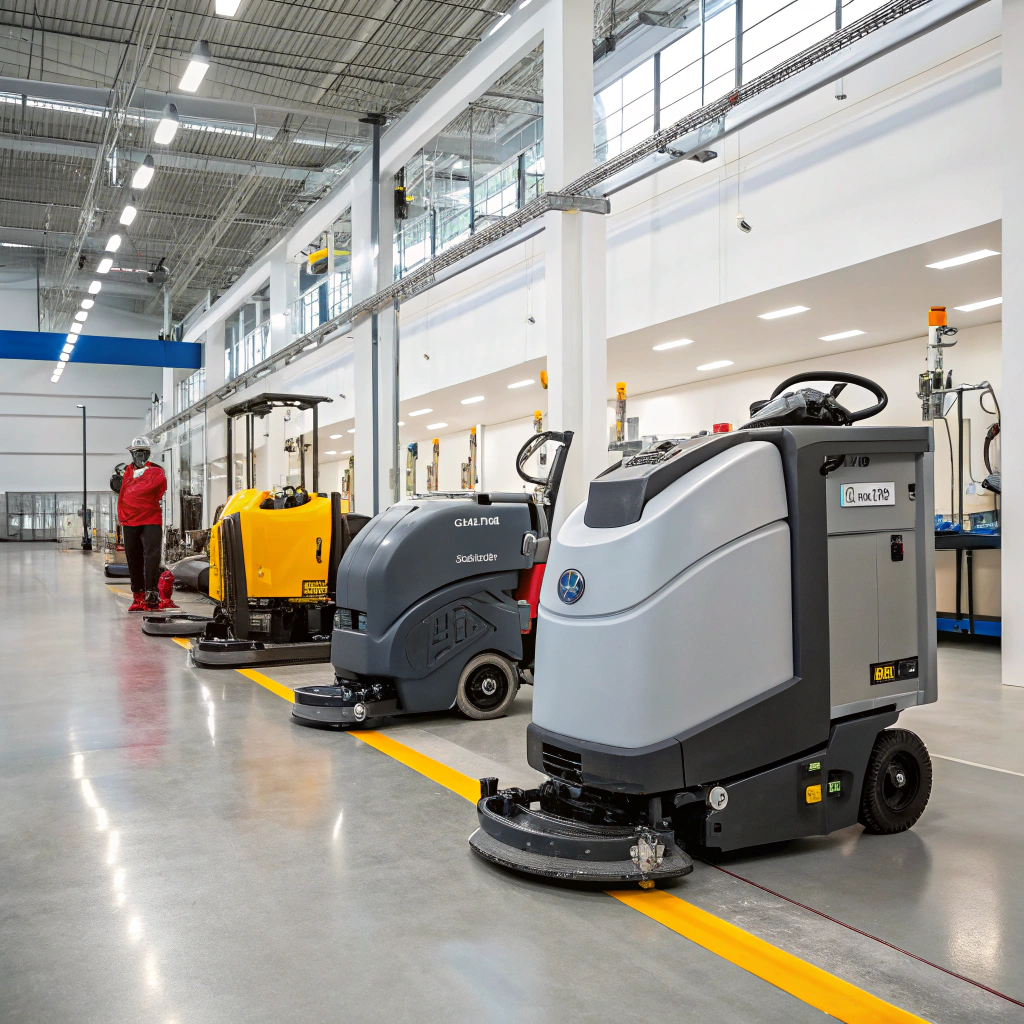
Your industrial cleaning investment directly impacts operational efficiency, with proper maintenance reducing facility downtime by up to 35% annually. You’ll need to implement a systematic cleaning protocol that integrates OSHA-compliant procedures, specialized equipment calibration, and eco-friendly solutions. By maintaining regular service intervals and documenting all cleaning processes, you’re ensuring both regulatory compliance and peak facility performance in Orange County’s industrial sector.